Hydraulic dredging is one of the most effective methods for sediment removal. It relies on powerful suction and pumping systems to transport materials through pipelines. Unlike mechanical dredging, which physically scoops sediment, hydraulic dredging uses water as a transport medium to move sand, silt, and other materials over long distances. This process is essential for maintaining waterways, restoring shorelines, and supporting mining operations. However, the efficiency of hydraulic dredging largely depends on the design and management of the pipeline transport system.
Proper pipeline design is crucial for preventing blockages and ensuring optimal flow rates. Factors such as pipeline diameter, material composition, and layout directly impact dredging efficiency. A well-planned system reduces sediment settling, minimizes friction loss, and prevents unnecessary wear on dredging components. The hydraulic dredge pump is at the heart of this system, generating the pressure needed to keep sediment moving consistently.
Advancements in hydraulic dredge pump technology, such as variable speed drives and high-efficiency impellers, have significantly improved sediment transport capabilities. By optimizing pump performance and pipeline design, operators can enhance dredging efficiency, reduce downtime caused by blockages, and lower maintenance costs. In this article, we will explore the best practices for managing sediment flow, selecting the right equipment, and utilizing advanced dredging technologies to maximize performance in hydraulic dredging projects.
1. Understanding Pipeline Transport in Hydraulic Dredging
Pipeline transport is a critical component of hydraulic dredging. It enables the movement of sediment from the dredging site to designated discharge locations. This method uses a continuous flow of water to transport sand, silt, and other materials through pipelines, reducing the need for manual handling and making sediment removal more efficient. The effectiveness of hydraulic dredging depends on the pipeline system’s design, flow dynamics, and pump performance.
Key Components of a Dredging Pipeline System
- Hydraulic dredge pump – The central element that generates suction and pressure to transport sediment. A well-matched pump ensures a steady slurry flow while preventing clogging and excessive wear.
- Suction pipeline—This pipeline, Connected to the dredger, draws in sediment and water and directs it toward the pump.
- Discharge pipeline – This transports dredged material to a designated disposal or processing site. Its length, diameter, and material impact efficiency.
- Booster pumps—These additional pumps are Used in long-distance dredging projects. They help maintain consistent pressure and prevent blockages in extended pipelines.
Factors Influencing Sediment Transport
Several factors determine how efficiently sediment moves through the pipeline system in hydraulic dredging:
- Flow velocity – Maintaining an optimal flow rate is crucial to prevent sediment from settling and forming blockages.
- Pipeline diameter – The right pipeline size reduces resistance while ensuring efficient sediment movement.
- Material composition – Different sediment types require different pipeline materials and pump configurations to prevent wear and clogging.
By optimizing these factors and ensuring the hydraulic dredge pump operates at peak efficiency, dredging operations can maximize sediment transport while minimizing maintenance issues and downtime.
2. Common Challenges in Sediment Transport
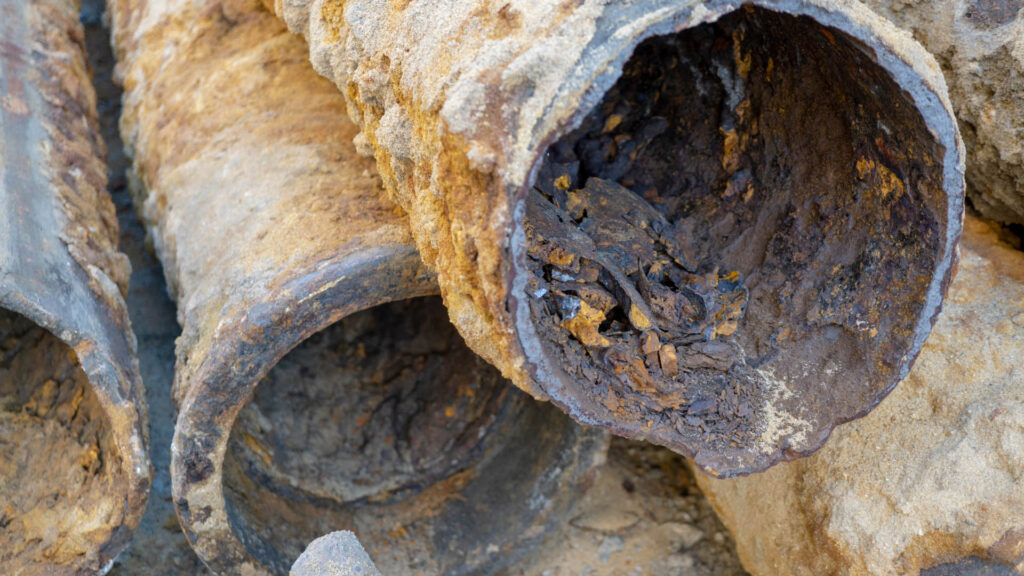
Efficient sediment transport is essential for successful hydraulic dredging operations, but various challenges can reduce efficiency, increase maintenance costs, and cause project delays. Understanding these common issues helps operators optimize dredging performance and prevent costly downtime.
Pipeline Blockages: Causes and Consequences
Blockages are one of the most significant challenges in sediment transport. They occur when sediment settles in the pipeline due to insufficient flow velocity or improper pipeline design. This can lead to reduced productivity, increased equipment wear, and unplanned maintenance downtime. A properly configured hydraulic dredge pump ensures continuous flow by maintaining the right pressure and preventing excessive sediment buildup.
Sediment Settling and Reduced Flow Efficiency
If flow velocity drops below the critical level, heavier particles begin to settle, creating obstructions that reduce pipeline capacity. This is particularly problematic in long pipelines or low-gradient sections where water velocity naturally slows. Adjusting the pump speed and incorporating booster pumps in extended pipelines can help maintain proper flow in hydraulic dredging systems.
Wear and Tear on Pipelines and Hydraulic Dredging Components
Pipelines and pumps experience significant abrasion due to continuous exposure to sand, gravel, and other materials. High-wear areas, such as bends and joints, are particularly vulnerable. Using wear-resistant materials and optimizing the impeller design in the hydraulic dredge pump can help extend the equipment’s lifespan and reduce maintenance needs.
Managing Varying Sediment Types
Different sediment compositions impact dredging efficiency. Coarse materials require more powerful suction and durable pipelines, while fine-grained materials can increase turbidity and reduce visibility. Proper equipment selection and monitoring help ensure that hydraulic dredging operations effectively handle diverse sediment types.
3. Optimizing Hydraulic Dredge Pump Performance for Pipeline Transport
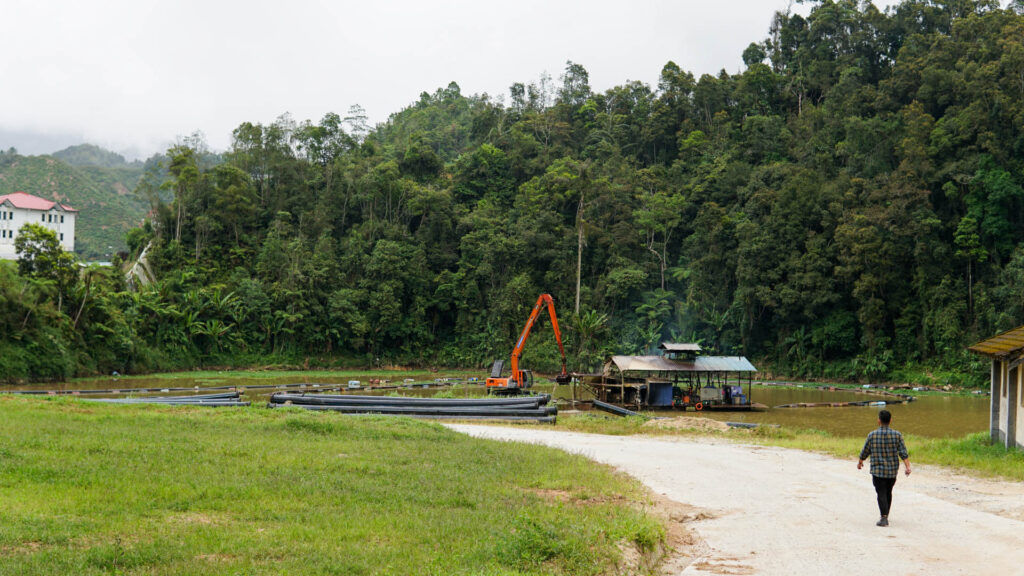
Efficient pipeline transport in hydraulic dredging depends largely on the performance of the hydraulic dredge pump. The right pump selection, impeller design, and operational adjustments can significantly improve sediment movement, reduce blockages, and enhance overall dredging efficiency.
Selecting the Right Hydraulic Dredge Pump
Different sediment types require different pump configurations. Coarse materials, such as gravel and compacted sand, demand a high-power hydraulic dredge pump with a reinforced impeller and wear-resistant casing. For fine-grained sediment, a pump with optimized slurry flow capabilities helps maintain a steady transport rate while preventing excessive turbulence. Additionally, transport distance plays a role—longer pipelines may require larger pumps or booster stations.
Impeller Design, Pump Speed, and Pressure
The impeller is a key component in maintaining flow efficiency. An improperly designed impeller can lead to clogging, reduced suction, and inefficient sediment transport. Adjusting pump speed and pressure is also critical—operating at too high or too low a speed can either damage equipment or cause sediment settling.
Variable Frequency Drives (VFDs) for Real-Time Adjustments
VFDs allow operators to adjust pump speed based on real-time dredging conditions. By optimizing motor output, VFDs improve energy efficiency, prevent cavitation, and enhance flow control in hydraulic dredging pipelines.
The Role of Booster Pumps
In long-distance dredging projects, booster pumps maintain consistent pressure along the pipeline. These additional pumps ensure continuous sediment movement, reducing the risk of blockages and increasing overall system efficiency. By strategically placing booster pumps, dredging operations can extend their reach while minimizing energy consumption.
4. Pipeline Design and Configuration Strategies
Proper pipeline design is essential for ensuring smooth and efficient sediment transport in hydraulic dredging operations. The right configuration minimizes blockages, reduces component wear, and maximizes the hydraulic dredge pump’s performance. By optimizing pipeline diameter, layout, and materials, operators can improve efficiency and reduce maintenance costs.
Determining Optimal Pipeline Diameter and Length
The pipeline’s diameter and length significantly impact dredging performance. If the diameter is too small, friction loss increases, reducing flow efficiency and putting excessive strain on the hydraulic dredge pump. Conversely, oversized pipelines can cause sediment to settle, leading to blockages. A well-balanced pipeline diameter, based on the type of sediment and pump capacity, ensures smooth transport. Additionally, longer pipelines may require booster pumps to maintain adequate pressure throughout the system.
Impact of Pipeline Bends and Layout on Flow Efficiency
Pipeline bends and sharp turns disrupt sediment flow, increasing friction and the likelihood of blockages. Whenever possible, pipeline layouts should minimize sharp bends and use gradual curves instead. Gentle transitions maintain a steady flow and reduce pressure fluctuations in hydraulic dredging systems.
Best Practices for Reducing Friction Loss
Reducing internal friction within the pipeline is essential to maintaining high transport rates. Smooth-walled pipes, optimizing pump pressure, and ensuring a consistent flow rate help minimize energy loss and improve dredging efficiency.
Material Selection for Durability
Pipelines experience constant wear from abrasive sediments. Using high-density polyethylene (HDPE), rubber-lined steel, or reinforced composite materials extends pipeline lifespan and reduces maintenance. Selecting wear-resistant materials is crucial for improving long-term efficiency in hydraulic dredging projects.
5. Preventing and Managing Blockages in Dredging Pipelines
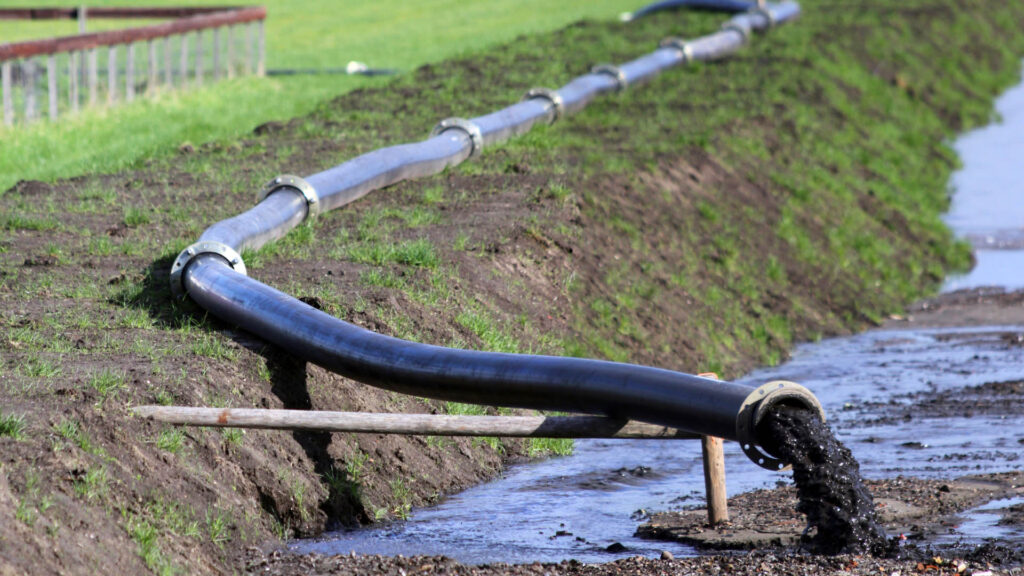
Blockages in dredging pipelines can significantly impact the efficiency and productivity of hydraulic dredging operations. A well-maintained pipeline system, combined with real-time monitoring and proactive maintenance strategies, can help prevent sediment buildup and ensure uninterrupted material transport.
Effective Pipeline Monitoring and Real-Time Diagnostics
Continuous monitoring is essential for identifying potential issues before they escalate into full blockages. Advanced hydraulic dredging systems now integrate automated diagnostics that track pipeline conditions in real time. Monitoring flow rates, pressure levels, and sediment concentration ensure early detection of abnormalities that could indicate clogging.
Use of Pressure Sensors, Flow Meters, and Sediment Concentration Monitors
Pressure sensors help detect sudden drops or increases in pressure, which often signal blockages or pipeline restrictions. Flow meters provide critical data on slurry movement, ensuring that the hydraulic dredge pump operates at optimal efficiency. Sediment concentration monitors allow operators to adjust pump speed and pipeline flow to maintain a steady transport rate, preventing excessive sediment buildup.
Best Practices for Flushing and Clearing Blockages
Regular pipeline flushing using high-velocity water or air bursts helps remove settled sediment before it hardens into a clog. Operators can also implement backflushing techniques, in which the hydraulic dredge pump temporarily reverses flow to dislodge obstructing materials.
Proactive Maintenance Strategies
Routine inspections, predictive maintenance scheduling, and using wear-resistant pipeline materials are essential strategies for minimizing downtime. Ensuring proper pipeline design and optimizing flow velocity further reduce the risk of blockages, keeping hydraulic dredging operations running smoothly and efficiently.
6. Advanced Technologies for Efficient Pipeline Transport
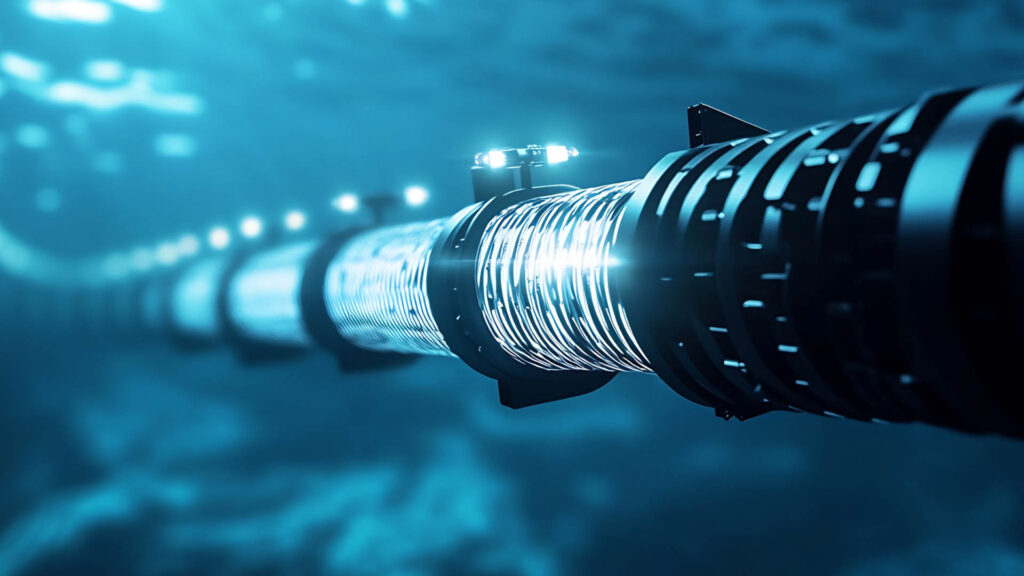
The integration of advanced technologies in hydraulic dredging has significantly improved pipeline transport efficiency. Automation, AI-driven maintenance, and GPS-based dredging software now enable more precise sediment transport while reducing downtime and operational costs. These innovations enhance the performance of hydraulic dredge pump systems and optimize flow management in complex dredging operations.
Automation and Remote Monitoring for Pipeline Flow Optimization
Automated pipeline monitoring systems provide real-time data on flow rates, pressure levels, and sediment concentration. By continuously tracking these parameters, operators can quickly detect irregularities and make necessary adjustments to maintain efficient sediment transport. Remote-controlled hydraulic dredging systems allow for real-time response to changing dredging conditions, improving overall performance and minimizing human intervention.
AI-Driven Predictive Maintenance for Hydraulic Dredge Pump Systems
Artificial intelligence (AI) is revolutionizing hydraulic dredge pump maintenance by predicting failures before they occur. AI-powered algorithms analyze historical and real-time performance data to identify wear patterns, cavitation risks, and potential blockages. By implementing predictive maintenance, dredging operations can reduce unexpected breakdowns, extend equipment lifespan, and optimize energy usage.
Integration of GPS and Dredging Software for Precise Material Transport
GPS and dredging software help operators track material movement with precision. These tools provide detailed mapping of dredging zones, allowing for targeted sediment removal and efficient pipeline transport. GPS-guided hydraulic dredging ensures that pipelines are correctly positioned for optimal flow, reducing energy consumption and improving project accuracy.
Future Innovations in Pipeline Materials and Sediment Management
Advancements in pipeline materials, such as reinforced composites and self-cleaning coatings, aim to reduce wear and prevent blockages. Emerging sediment management solutions, including automated slurry conditioning systems, will further enhance dredging efficiency and sustainability.
Conclusion
Optimizing pipeline transport in hydraulic dredging requires a strategic approach that includes proper equipment selection, pipeline design, and advanced monitoring technologies. Efficient sediment transport depends on maintaining the right flow velocity, reducing blockages, and minimizing pipeline wear. By implementing best practices such as optimal pipeline diameter selection, minimizing sharp bends, and using wear-resistant materials, dredging operations can achieve higher efficiency and reduced maintenance costs.
The hydraulic dredge pump is crucial for ensuring continuous sediment movement. Selecting the right pump based on sediment composition, transport distance, and operational demands helps prevent clogs and excessive wear. Incorporating booster pumps in long pipelines further enhances transport efficiency.
Adopting advanced monitoring systems, automation, and AI-driven predictive maintenance allows operators to track flow conditions in real time and prevent issues before they escalate. Remote monitoring, GPS-guided dredging, and smart sensors ensure optimal performance and cost savings. By investing in these modern solutions, dredging companies can improve operational reliability, reduce downtime, and extend the lifespan of their equipment, leading to more sustainable and productive dredging operations.