In the mining industry, efficient and reliable pumping systems are crucial for the successful extraction of minerals and the continuous operation of facilities. These mining pump solutions are responsible for transporting water, slurry, and chemicals necessary for various mining processes. Pumps play a vital role in dewatering mines, transporting slurry, and managing fluid flow in processing plants. Given the harsh operating conditions of mining environments, it is essential to implement pumping solutions that are not only efficient but also safe. This article highlights the challenges and solutions related to efficient and safe mining pump solutions in mining operations.
Key Challenges in Mining Pumping Operations
Mining operations present unique challenges for mining pump solutions, with specific concerns related to the materials handled, the operational environment, and industrial pumping safety. Below are the key challenges in mining pumping operations:
Handling Abrasive and Corrosive Materials
Mining operations typically deal with abrasive slurries that consist of a combination of water and solid particles. These slurries can be highly abrasive, leading to significant wear and tear on pump components. Additionally, some mining processes involve the use of corrosive chemicals, which can degrade pump materials over time. To address these challenges, mining pump solutions must be designed with durable materials like hardened steel or specialized coatings that resist both abrasion and corrosion. These systems also improve chemical handling efficiency, which is crucial for reducing equipment wear and downtime. Enhanced chemical handling efficiency not only prolongs the life of the equipment but also ensures smoother operations, minimizing potential interruptions.
Extreme Pressure and Depths
Pumping systems in mining operations often have to function under extreme pressure, especially in deep underground mines. Dewatering pumps, in particular, must operate at high pressure to remove water from deep mine shafts. This increases the risk of mechanical failure and requires mining pump solutions capable of handling such demanding conditions while maintaining both efficiency and industrial pumping safety.
Maintenance and Downtime
Downtime in mining operations can be costly, and pump failure is one of the primary causes of unexpected downtime. Mining pump solutions are exposed to constant wear and tear due to the abrasive materials they handle, which increases the need for frequent maintenance. Developing solutions that reduce maintenance requirements while ensuring reliability is critical to minimizing downtime and maintaining continuous operation.
Safety Concerns
Safety is always a top priority in mining operations, and pumping systems are no exception. The handling of hazardous materials, such as chemicals and flammable substances, poses significant safety risks. Pump systems must be designed with safety features that prevent leaks, spills, and other dangerous situations. Additionally, equipment malfunctions in a hazardous environment can put workers at risk, so industrial pumping safety protocols must be strictly adhered to.
Types of Pumps Commonly Used in Mining
Several types of pumps are specifically suited to the demanding conditions of mining operations. Each pump type offers distinct advantages depending on the application.
Centrifugal Slurry Pumps
Centrifugal slurry pumps are one of the most commonly used types of mining pump solutions. They are designed to efficiently transport slurries containing high concentrations of solids over long distances. These pumps use a rotating impeller to generate centrifugal force, moving the slurry through the system. Centrifugal slurry pumps are known for their durability and ability to handle abrasive materials, making them ideal for mining operations.
Positive Displacement Pumps
Positive displacement pumps are often used in applications where consistent flow and high pressure are required. These mining pump solutions move fluids by trapping a fixed amount of fluid and forcing it through the system. They are particularly effective in handling viscous fluids or slurries with a high solids content, which are common in mining. Positive displacement pumps are also reliable in high-pressure environments, making them ideal mining pump solutions for dewatering or slurry transport.
Peristaltic Pumps
Peristaltic pumps are highly effective for handling abrasive slurries and corrosive chemicals. These pumps work by compressing and releasing a flexible hose or tube to move fluid through the system, avoiding direct contact between the pump’s internal components and the slurry or chemicals. This reduces wear and tear, making peristaltic pumps low-maintenance and ideal for harsh mining conditions. Their ability to handle corrosive chemicals improves chemical handling efficiency, reducing downtime caused by material degradation.
Submersible Pumps
Submersible pumps are essential for dewatering mining shafts and handling water in deep, difficult-to-reach areas. These pumps are designed to operate while fully submerged in water, making them highly effective in managing flooding and removing groundwater. Their sealed design prevents water from damaging the pump motor, allowing them to function efficiently in deep or submerged environments. Submersible pumps also enhance both operational efficiency and industrial pumping safety.
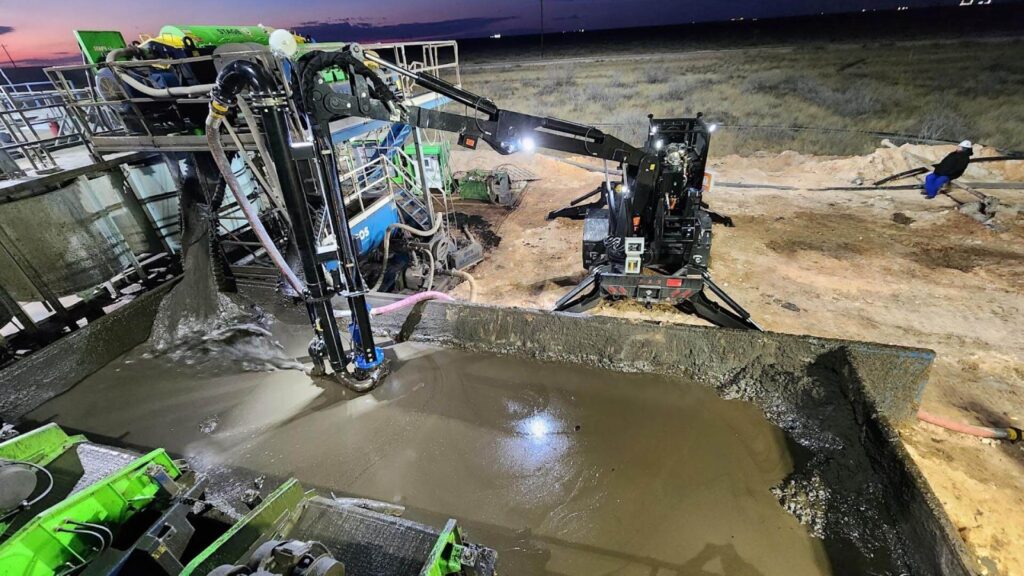
Enhancing Efficiency in Mining Pumping Operations
Maximizing efficiency in pumping systems can lead to significant cost savings and reduced downtime. Here are a few ways mining operations can improve pumping efficiency:
Variable Frequency Drives (VFDs)
Variable Frequency Drives (VFDs) allow for precise control over pump speed, optimizing energy consumption by matching pump output to actual demand. By adjusting the motor speed, VFDs can reduce energy usage, especially in situations where the full capacity of the pump is not required. This not only improves energy efficiency but also extends the life of the pump by reducing wear and tear. VFDs play a significant role in optimizing mining pump solutions for both energy efficiency and performance.
Automated Monitoring Systems
Implementing automated monitoring systems can provide real-time data on pump performance, enabling proactive maintenance and preventing unexpected failures. These systems track key performance indicators such as flow rate, pressure, and temperature, allowing operators to identify potential issues before they become critical. Automated monitoring helps ensure that mining pump solutions are operating efficiently and can reduce downtime by scheduling maintenance when it is most convenient. This enhances both chemical handling efficiency by ensuring accurate chemical flow and reducing waste. Additionally, improved chemical handling efficiency not only minimizes wear on pump components but also helps maintain consistent performance, further optimizing operations. The focus on chemical handling efficiency and overall safety in mining pump solutions makes them more reliable and effective for long-term mining operations.
Pump Design and Material Improvements
Advances in pump design and materials can also improve efficiency and durability. By using materials like hardened steel, ceramics, or specialized coatings, modern pumps can withstand the harsh conditions of mining operations for longer periods without requiring frequent maintenance. Additionally, pump designs that minimize the number of moving parts or eliminate contact between pump components and abrasive materials can further enhance performance, reducing downtime and improving chemical handling efficiency.
Safety Considerations in Pumping Solutions
Safety is paramount in mining operations, and mining pump solutions must be designed with safety features to protect both workers and equipment. Ensuring industrial pumping safety is critical to preventing accidents and maintaining a secure working environment in such high-risk settings.
Explosion-Proof and Intrinsically Safe Pumps
In hazardous environments where flammable gases or chemicals are present, explosion-proof and intrinsically safe pumps are critical. These pumps are designed to operate safely in environments where ignition could occur, preventing explosions or fires. They are essential in mining operations where volatile substances are present, ensuring industrial pumping safety is maintained.
Regular Maintenance and Inspection
Regular maintenance and inspection of pumping systems are crucial for preventing accidents and ensuring safe operation. Maintenance programs should include routine checks of pump components, seals, and electrical systems to identify and address potential hazards before they lead to equipment failure or safety incidents. This proactive approach ensures that mining pump solutions continue to operate efficiently and safely.
Operator Training
Having properly trained personnel is essential for the safe operation of pumping systems. Operators must be knowledgeable about pump functions, safety protocols, and emergency procedures. Proper training ensures that workers can operate pumps efficiently and respond appropriately to any safety concerns or equipment malfunctions. Well-trained operators contribute significantly to both the efficiency and safety of mining pump solutions.
Conclusion
Efficient and safe pumping systems are critical to the success of mining operations. By addressing the unique challenges of mining, such as handling abrasive materials and operating under extreme conditions, modern mining pump solutions can enhance both productivity and safety. Looking forward, innovations like Variable Frequency Drives and automated monitoring systems will continue to drive improvements in energy efficiency and operational reliability. To ensure long-term success, mining operations must invest in advanced and reliable pumping systems that balance both efficiency and safety, ensuring both chemical handling efficiency and industrial pumping safety are prioritized.